For the past 50 years, L&H has always looked for ways to improve machine uptime and operation’s productivity. Field tested L&H designs have proven increased life, better safety and decreased downtime and maintenance. One of our most significant engineered solutions is currently being redesigned into the next generation of engineered upgrades using new technology improvements. With over 100 undercarriages of our current design operating across the globe, and proven to last at least 30% longer than OEM models, the new L&H undercarriage will leap further ahead of existing technologies.
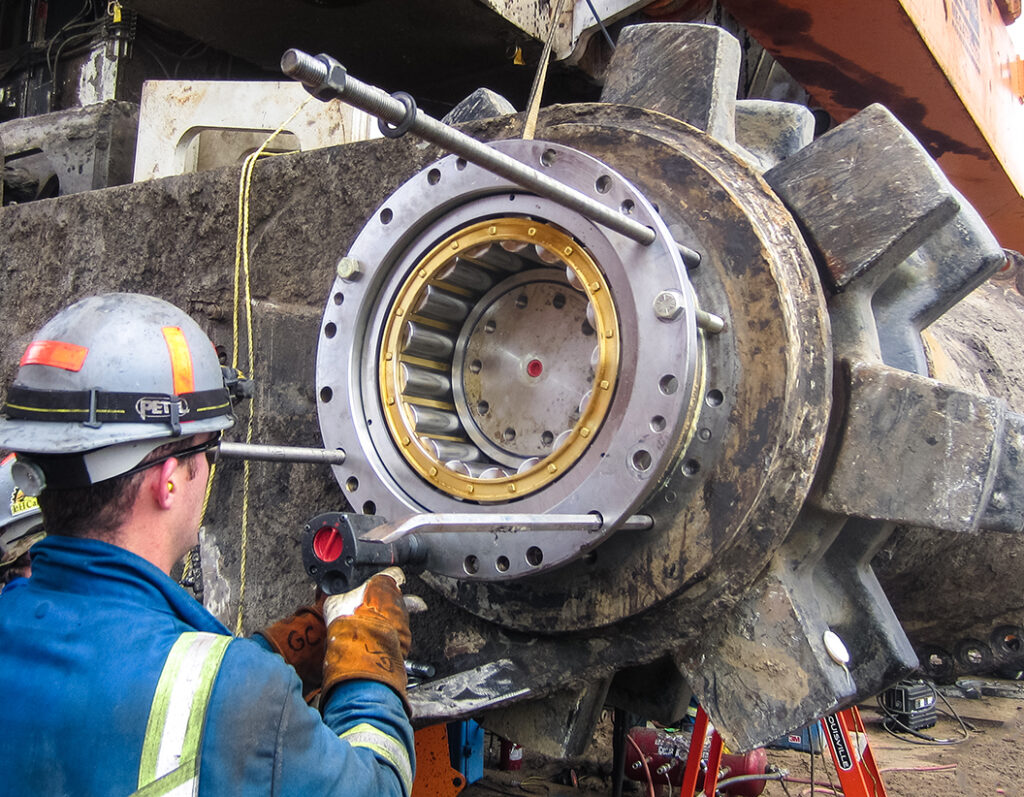
Derived from customer partnerships
After examining worn out and failed OEM parts, L&H engineers gathered knowledge about what failed and why. Many times, the conclusion illustrated design faults in the OEM designs. L&H engineers knew they could improve the designs and help customers experience longer life. Customer’s helped drive the L&H solution over the years, coming to L&H with issues that needed a unique and careful solutions. Steve Metzger, L&H design engineer, explained,
“At L&H, if we see a clear advantage to a design, we offer it as an upgrade. Often times the OEM’s are confined by design standards, and must follow the previous work, at L&H we are not confined and can offer custom solutions for our customers.”
After observing similar needs in the industry on customer machines, L&H decided to build their own solution, the L&H undercarriage has changed the way customers maintenance their machines, increased safety, and provided more reliable machines.
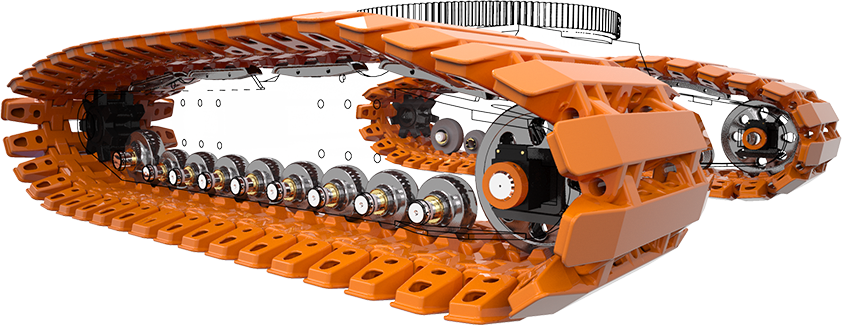
Redesigning key structures and utilizing upgraded materials
Looking at existing OEM designs, L&H engineers have evaluated the most costly pitfalls of current market offerings and addressed these issues with the upgraded system in a number of ways. Bill Schroyer, L&H Engineering Manager commented,
“We want to take the best aspects of all of our current designs, get rid of the bad, add innovative and new ideas to continue to make the best possible undercarriage we can come up with for any shovel model.”
- Manganese steel—a work hardened material, superior to all others— was used to build shoes for both CAT® and Komatsu shovels.
- Larger pins and wider hinges were used at the clevis of the shoe to slow the pitch change and extend the life of the track.
- Building a high-performance, deep engagement track system for both CAT and Komatsu machines that reduces wear to tumblers.
- Load rollers are deep hardened to prevent wear and future spalling of the surface. Reducing loss to the diameter, the rollers keep the crawler structures up off the shoes for and extended lifetime.
- Fitted bearings on the two outer support blocks, creates twice the support, sharing half the load between both bearings. The wheel is then fixed to the shaft, helping the wheel to remain stable between both bearing blocks, adding life and reliability to the system.