A Canadian mine’s 2570W dragline was in need of repairs to the hoist machinery and structures. The machine’s components had reached life expectancy and needed to be replaced. General maintenance throughout the mechanical assemblies was required from replacing boom lacing and point sheaves to repairing cracks and re-machining. When the mine selected L&H Industrial for the job; it was the company’s first time working with the mine and L&H was eager for the opportunity. Account Manager, Scott Wedertz explained,
“We had to make it count; we wanted to demonstrate what kind of company we were and create a long term partnership focused on quality, safety, service, and innovation. We were grateful for the opportunity to work with the mine and wanted to be invited back.”
Quality | Safety | Service | Innovation
L&H’s field team spent over 40 days on site prepping the machine for the outage and installing components including specific L&H design innovations. A newly redesigned cross beam for the boom point assembly was installed as well as an upgraded deck-lug for the boom foot connection, and a rebuilt boom point swivel.
The original OEM deck-lug design was prone to inherent cracking throughout the “box-type” construction of welded plate; requiring repairs and eventually the need to completely replace the lug. L&H installed a single solid piece forged lug that illustrates a decrease in stress risers through FEA analysis. Wedertz stated, “We believe the combined upgrades and rebuilt components installed will decrease maintenance and extend life for the machine.”
Upon completion of the outage, Wedertz described his thoughts on the result of the finished project, “I believe this project was seamless in its execution because of the amount of time we spent collaborating and planning with the mine in preparation for the job; it was crucial to the success of the project.”
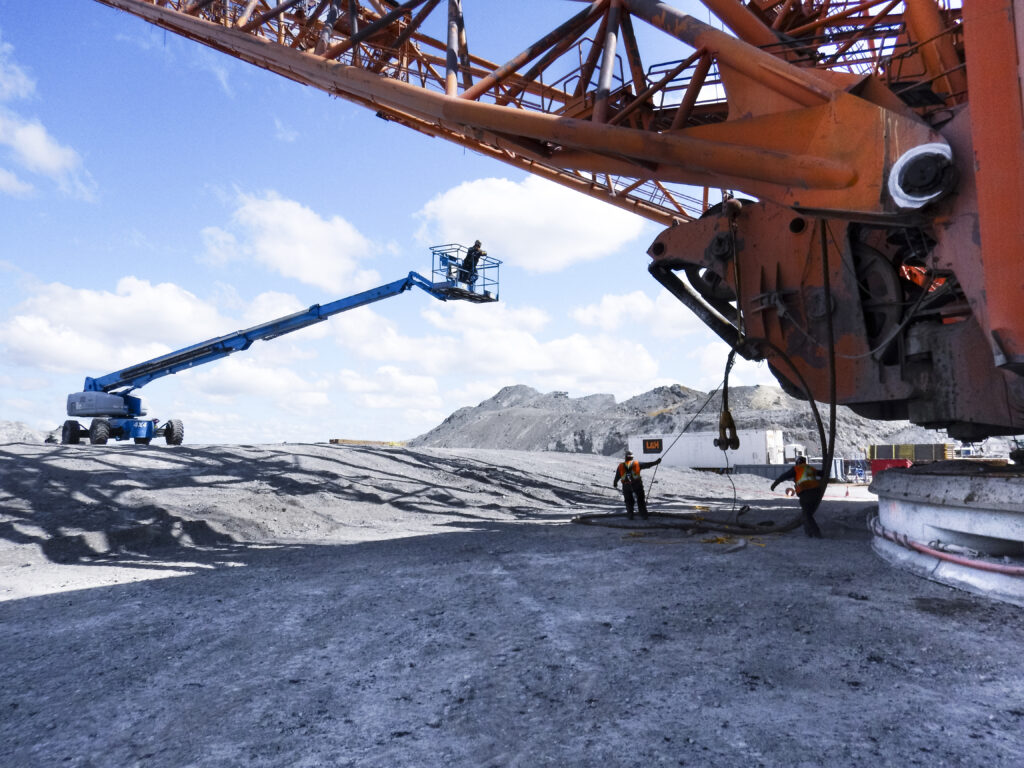